In today’s rapidly evolving industrial landscape, advanced technologies are revolutionizing the manufacturing sector, driving efficiency, reducing costs, and creating opportunities for sustainable growth. By integrating cutting-edge digital solutions, manufacturers worldwide are redefining their operations to stay competitive in the global marketplace. This transformation is fueled by innovations such as real-time data processing, interconnected systems, and smart technologies that eliminate traditional bottlenecks.
From Paper to Pixels: The Digital Factory Revolution
The Digital Factory is the cornerstone of modern manufacturing. Traditional paper-based processes are now obsolete. In their place, a seamless, interconnected system enables direct interactions between equipment and software, reducing human error and optimizing efficiency.
-
Streamlined Operations: The Digital Factory minimizes manual interventions by establishing a singular source of truth. Data flows effortlessly across all levels, ensuring accuracy and consistency. Workers no longer rely on individual expertise to interpret and transfer information; software solutions now serve as the backbone of decision-making.
-
Real-Time Metrics: Supervisors and managers are empowered with immediate insights into operations. Instead of analyzing yesterday’s data or waiting for morning reports, they can make informed decisions in real time, enabling quicker responses to dynamic production challenges.
-
Connected Ecosystems: The Digital Factory thrives on a robust, interconnected ecosystem where equipment integrates with Supervisory Control and Data Acquisition (SCADA), Manufacturing Execution Systems (MES), Enterprise Resource Planning (ERP), and the cloud. This interconnectivity fosters a collaborative environment that drives efficiency across the board.
Leveraging Data for Operational Excellence
The foundation of digital manufacturing lies in acquiring and utilizing data effectively. The key steps to achieving this transformation include:
-
Data Acquisition Across Edges: Capturing data from every machine, process, and operational touchpoint ensures a comprehensive understanding of the production environment.
-
Actionable Insights: Once collected, this data is processed to generate actionable insights. Advanced analytics tools sift through large datasets, identifying trends and anomalies that inform decision-making and strategy.
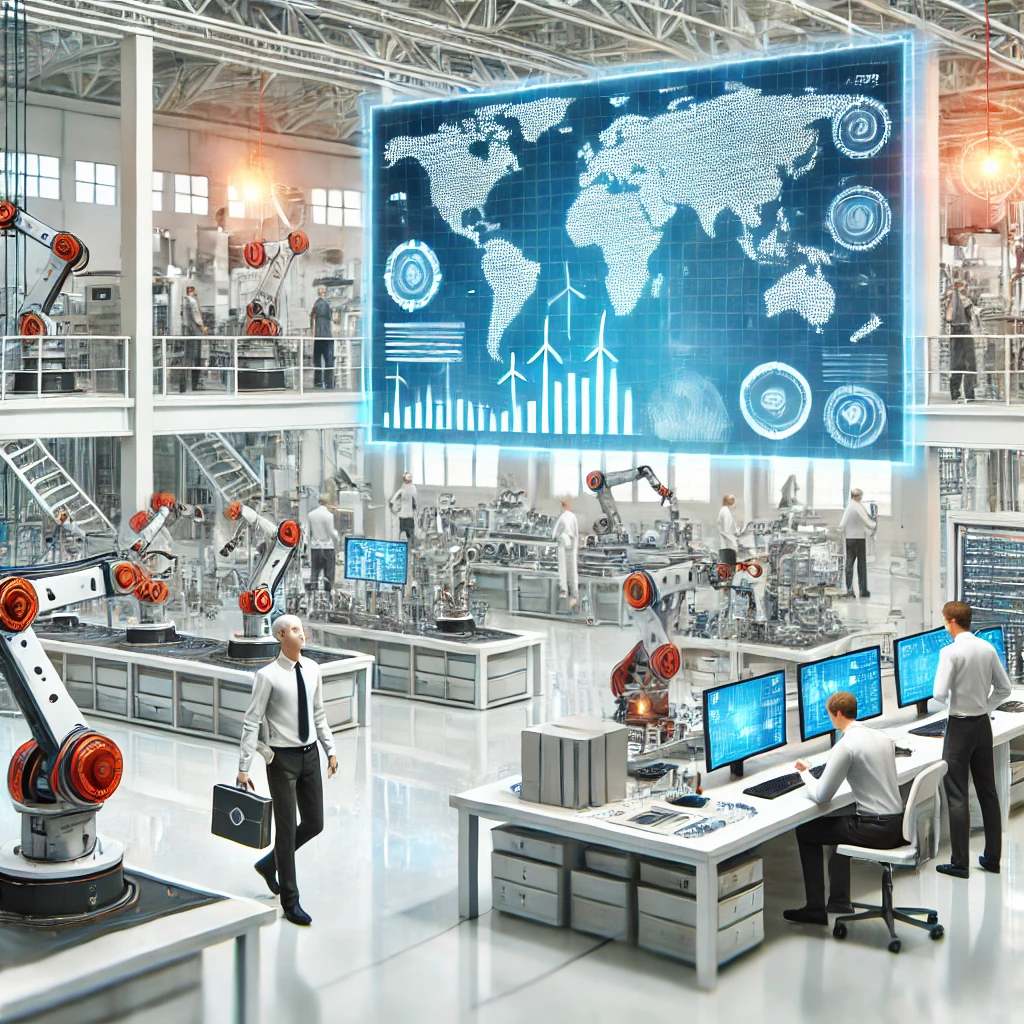
The Era of Smart Manufacturing
The integration of advanced technologies brings unparalleled predictability, adaptability, and scalability to manufacturing operations. These enhancements include:
-
Digital Twins: Virtual replicas of physical processes and equipment enable manufacturers to simulate scenarios, test hypotheses, and predict outcomes without disrupting actual operations. This capability reduces downtime and accelerates innovation.
-
Connected Supply Chains: Interconnected machines, factories, and supply chains create a cohesive manufacturing ecosystem that improves efficiency and reduces waste. Data aggregation across all levels allows for synchronized operations, ensuring smooth production workflows.
-
Automation and Adaptability: With connected systems, factories can adapt quickly to changes in demand or supply chain disruptions. Machines are programmed to respond autonomously to production needs, enhancing overall resilience.
Building the Future: Solutions for Tomorrow’s Manufacturing Needs
Manufacturers need tools that prepare them for future challenges. Advanced digital platforms address key areas of need:
- Design-Fabrication Link: Seamlessly bridge the gap between design and production with digital tools that enable rapid prototyping and iteration.
- Actionable Data Insights: Harness aggregated data to drive decisions, improve quality, and meet sustainability goals.
- Business Resilience: Future-proof designs and processes create resilience, empowering manufacturers to adapt to market dynamics and evolving demands.
Core Services Driving the Transformation
Industrial IoT (Internet of Things): The backbone of connected manufacturing, IoT technologies enable machines to communicate, monitor performance, and optimize processes without human intervention.
Manufacturing Operations Management: A comprehensive approach to overseeing and enhancing manufacturing activities. This service streamlines workflows, ensuring consistency and quality.
Digital Factory Solutions: These provide the framework for seamless integration of digital tools and physical processes, making operations more efficient and data-driven.
Digital Twins: Virtual modeling allows for precise simulations, offering invaluable insights into potential optimizations before implementing changes in the real world.
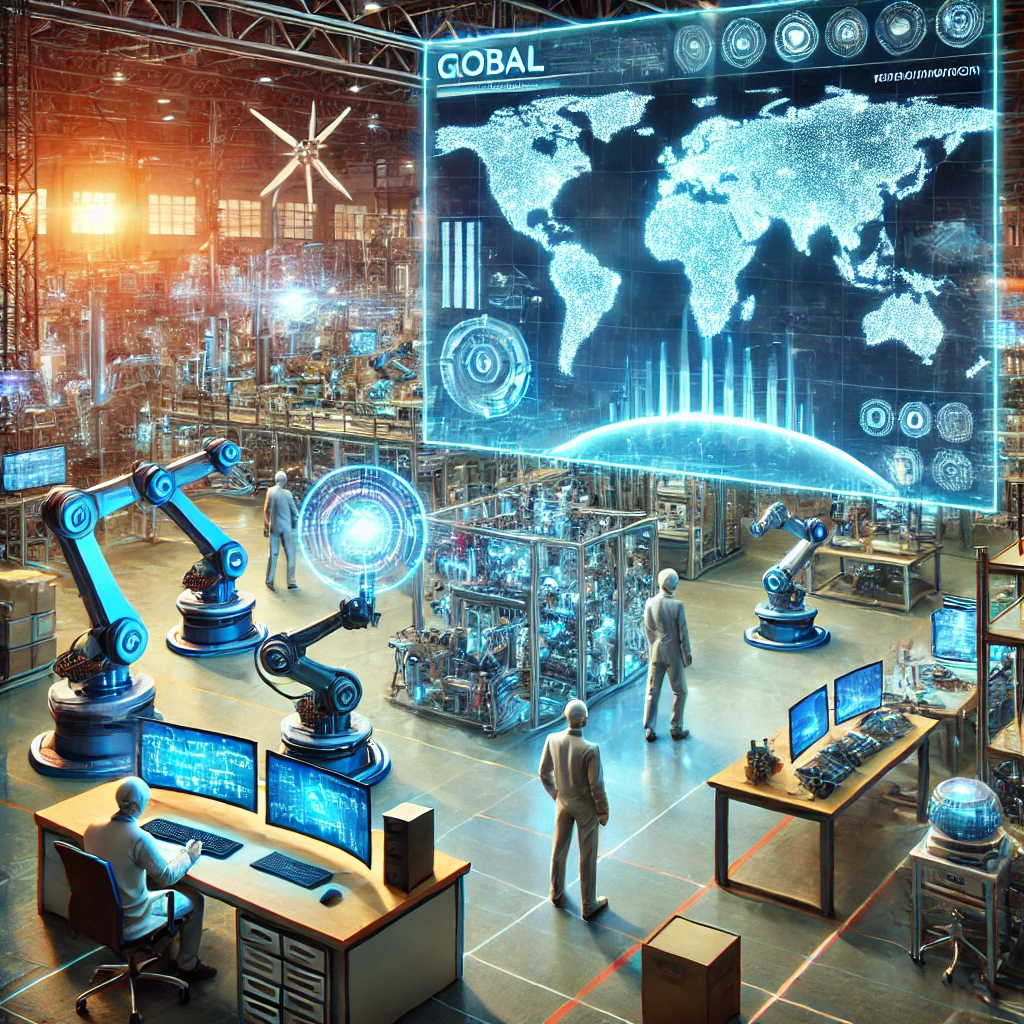
Enabling Competitive Advantage with Proven Solutions
By leveraging intuitive and robust tools, manufacturers can achieve significant improvements in efficiency and productivity. These solutions include:
- Enterprise Resource Planning (ERP): Comprehensive systems that integrate all facets of manufacturing, from inventory management to financial planning.
- Advanced Planning & Scheduling (APS): Tools like Siemens APS enhance precision in production planning, ensuring optimal use of resources and time.
- Business Intelligence with Qlik: Data visualization and analytics enable businesses to uncover insights that drive smarter decisions.
- Industry 4.0 Adoption: The fusion of automation, IoT, and advanced analytics defines the future of manufacturing, creating smarter, more agile operations.
Conclusion
The integration of advanced technologies into manufacturing is no longer optional—it is imperative. Digital transformation not only enhances operational efficiency but also creates a sustainable, scalable future for global manufacturing. By adopting a Digital Factory model, businesses can leverage real-time metrics, interconnected systems, and actionable insights to redefine competitiveness in the global arena.
As manufacturers embrace Industry 4.0, the seamless convergence of physical and digital realms offers boundless opportunities. The journey towards this transformation is not just about technology; it is about unlocking new potential, fostering innovation, and reshaping the future of manufacturing.