In the fast-paced tire industry, being efficient and cutting downtime is key. Enterprise Resource Planning (ERP) solutions are changing the game. They help tire makers work better and faster.
Tire ERP systems are not just any business software. They have special features for tire producers. These tools help manage inventory, make production smoother, and improve supply chain and customer service. They also cut down on costly downtime.
Why Tire Manufacturers Need Specialized ERP Solutions
Standard ERP systems often lack the specialized features needed for tire production, where even slight inefficiencies can lead to costly delays and customer dissatisfaction. Tire industry ERPs are designed to streamline operations specifically for tire production environments. By automating processes and offering real-time data visibility, these systems help manufacturers improve resource utilization, reduce downtime, and ultimately enhance customer satisfaction.
Key Components of Tire Industry ERP Systems
Modern ERP solutions for tire manufacturing integrate various business functions, including:
Inventory Management and Traceability: Real-time inventory tracking with tools like barcode scanning and predictive analytics ensures that stock levels are always optimized. This allows manufacturers to respond to fluctuating demand quickly, reducing downtime and preventing overstock issues.
Production Planning and Scheduling: Advanced ERP systems support complex production schedules by coordinating labor, materials, and machinery, making it easy to manage order priorities and reduce bottlenecks.
Quality Control and Compliance: Quality management modules ensure that products meet safety and compliance standards, reducing the risk of defects and recalls.
Predictive Maintenance: By using ERP-enabled predictive maintenance, manufacturers can avoid unexpected machinery failures, extend equipment life, and reduce repair costs.
Customer Relationship Management (CRM): Integrated CRM tools streamline order management, giving manufacturers a unified view of customer profiles, order histories, and preferences for better service.
These functionalities help tire manufacturers improve their overall performance, from production efficiency to customer experience, leading to growth in a competitive market.
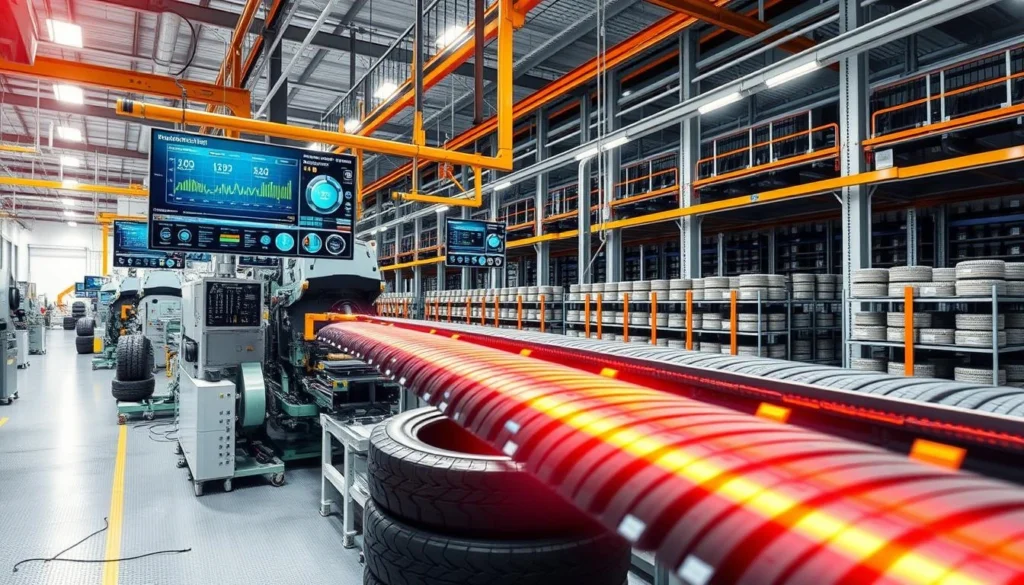
Streamlining Inventory Management with Digital Tools
In the tire industry, managing inventory well is key. It helps avoid downtime, ensures on-time deliveries, and keeps stock levels just right. Modern digital tools in ERP solutions make this task easier.
These digital tools offer real-time inventory control. They use sensors, barcodes, and cloud tracking. This lets tire makers keep an eye on their stock levels as they change. They can then make smart choices fast.
Using these digital tools, tire makers get a clear view of their inventory management. This leads to less downtime, happier customers, and better efficiency overall.
“Effective inventory management is the backbone of a successful tire manufacturing operation. With the right digital tools, tire companies can streamline their processes and stay ahead of the competition.”
Real-Time Production Monitoring and Control Systems
In the fast-paced world of tire manufacturing, real-time monitoring and control systems are key. They boost efficiency and cut downtime. Tire Industry ERP solutions offer advanced tools that streamline the production process.
Production Floor Data Collection
Advanced ERP systems work well with the production floor. They collect real-time data from sensors and systems. This data includes machine performance, material usage, and worker productivity.
By using this information, tire manufacturers can make better decisions. They can optimize the production process.
Quality Control Integration
Keeping quality high is crucial in the tire industry. ERP solutions add quality control to the production workflow. This allows for automated inspections and testing at key points.
This ensures any defects or issues are caught and fixed quickly. It reduces the risk of costly recalls or unhappy customers.
Automated Alert Systems
ERP systems have advanced alert systems. They notify managers and operators of potential problems or production issues. These automated alerts can be set off by many things, like equipment failures or material shortages.
By quickly addressing these issues, tire manufacturers can avoid production delays. They can keep the tire-building process smooth.
The use of real-time production control and quality control systems helps tire manufacturers. They can optimize operations, reduce downtime, and boost productivity. By using ERP technology, they can stay competitive and deliver top-quality products.
Automating Order Processing and Customer Management
In the tire industry, fast order processing and good customer management are key. Modern ERP solutions help with this, making things smoother and improving customer happiness. This keeps customers coming back.
ERP systems make order processing smooth. They use one place for all data and easy-to-use systems. This cuts down on mistakes and makes orders faster. It makes customers happier and helps businesses grow.
ERP also has CRM tools for managing customers. These tools help keep all customer info in one place. They let businesses understand what customers want and need. This way, tire companies can offer better service and build stronger relationships with customers.
Key Benefits of ERP-Powered Order Processing and Customer Management
Streamlined order entry and fulfillment
Improved order accuracy and reduced errors
Enhanced customer experience and satisfaction
Centralized customer data and insights
Personalized service and targeted marketing
Increased customer loyalty and repeat business
ERP solutions change how tire companies handle orders and customers. They help businesses grow, make more money, and keep customers happy.
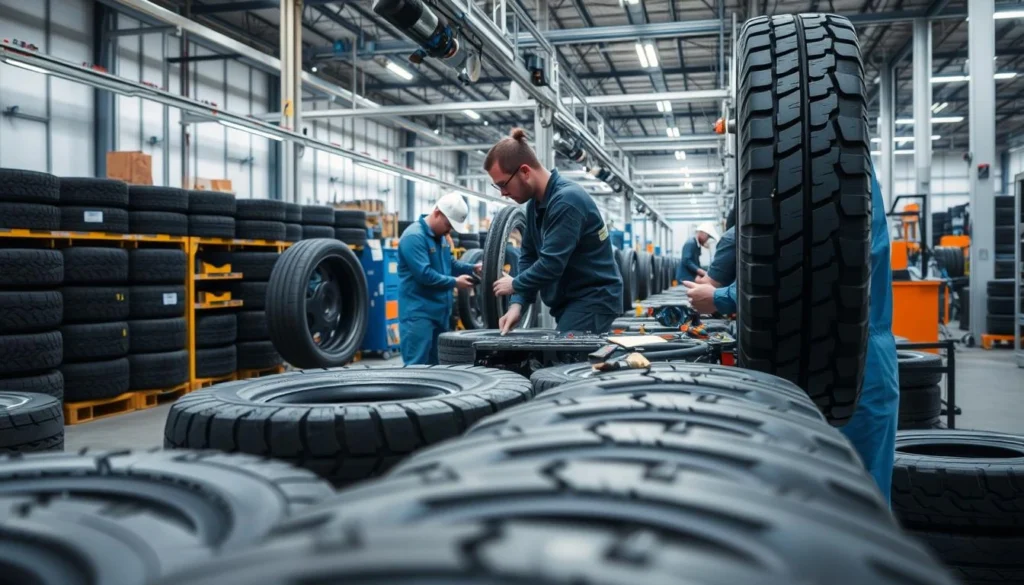
Cost Reduction Through Enhanced Resource Planning
Tire manufacturers can save a lot of money by using ERP solutions. These systems help optimize many areas of resource planning. This leads to big cuts in operational costs.
Material Usage Optimization
ERP systems give tire makers detailed insights into material use. This data helps manage inventory better, cutting down on waste. By improving material use, tire makers can lower their costs and achieve cost reduction.
Labor Resource Management
Managing labor well is key for tire makers. ERP solutions help plan and schedule workforces better. This aligns labor with production needs, saving on overtime and boosting efficiency.
Energy Consumption Control
Energy costs are a big expense in tire making. ERP systems offer deep insights into energy use. This lets tire makers find and fix high energy consumption spots. With smart planning, they can cut energy costs a lot.
ERP solutions open up many ways for tire makers to save money. They help with material, labor, and energy use. These tools help tire producers cut costs and increase profits.
Implementing Preventive Maintenance Schedules
In the fast-paced world of tire manufacturing and servicing, it’s key to have good preventive maintenance schedules. This helps reduce downtime and makes equipment work better. Tire Industry ERP solutions make this easier, helping tire shops and service centers stay on top.
ERP for preventive maintenance lets businesses use data to plan better. They can see how their equipment is doing in real time. This way, they can plan maintenance ahead of time, avoiding big problems and saving money.
Also, ERP systems can predict when maintenance is needed. They use past data and how often equipment is used. This means technicians can fix things when they need to, not when they break down.
Data-Driven Decision Making for Tire Manufacturers
In the competitive tire industry, data-driven decision making is key. Tire makers who use Enterprise Resource Planning (ERP) solutions make better choices. This leads to more efficiency and profit. Key parts of this approach are performance analytics and reporting, and forecasting and trend analysis
Performance Analytics and Reporting
ERP systems give tire makers detailed performance analytics and reporting. These tools help track important metrics like production, inventory, and sales. By looking at all this data, tire makers can see how their business is doing and find ways to improve.
Forecasting and Trend Analysis
With the data from their ERP systems, tire makers can use advanced forecasting and trend analysis. These tools help predict market needs and plan production. By studying past trends, tire makers can get ready for changes in demand and adjust their operations.
Using data-driven decision making in tire industry ERP solutions helps businesses adapt fast to market changes. This leads to better processes and growth. By using analytics, reporting, forecasting, and trend analysis, tire makers can make smart decisions. This improves their efficiency and profit.
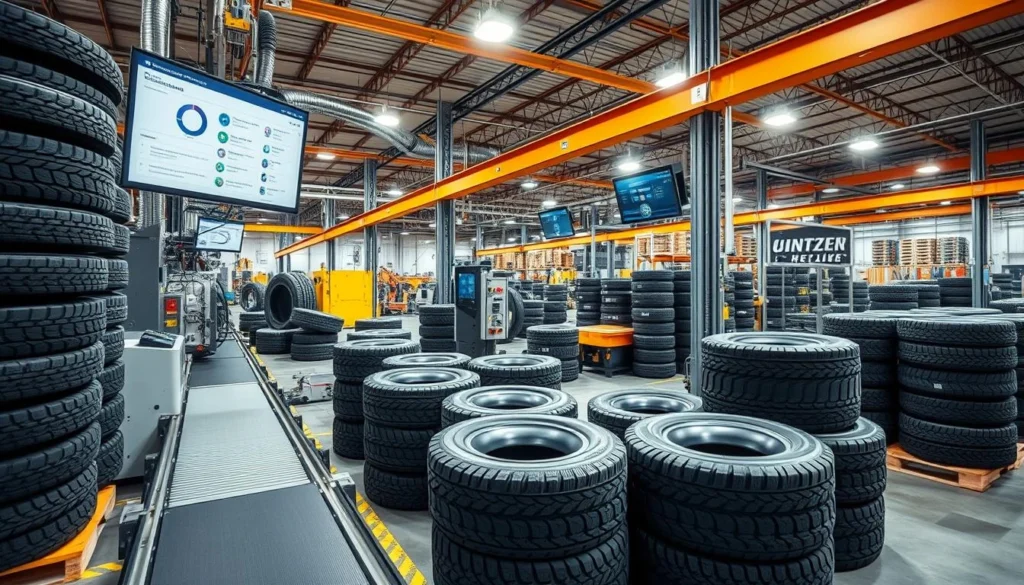
Enhancing Customer Service Through ERP Integration
In the fast-paced tire industry, delivering exceptional customer service is key. It helps build loyalty and drive business growth. Tire Industry ERP solutions offer a powerful platform to streamline customer-facing operations. This empowers tire dealers to provide a seamless and personalized experience.
Modern ERP systems integrate appointment scheduling tools. Tire dealers can now offer customers the convenience of booking service appointments online or through a mobile app. This reduces wait times and improves overall satisfaction. By synchronizing these schedules with back-end operations, technicians can better prepare for upcoming jobs and ensure timely completion.
ERP integration also enables tire dealers to access a comprehensive customer purchase history. This allows them to make informed recommendations and anticipate future needs. When a customer arrives for service, the dealer can quickly pull up their previous purchases, maintenance records, and preferences. This provides a tailored experience that builds trust and loyalty.
By integrating ERP solutions, tire dealers can also streamline their order processing and inventory management. This leads to faster turnaround times and more efficient customer interactions. The integration allows for real-time updates on product availability. This enables dealers to provide accurate information and deliver on their promises.
Through the strategic implementation of ERP systems, tire dealers can elevate their customer service. This fosters strong relationships and positions their business for long-term success in the competitive tire industry.
Future-Proofing Your Tire Manufacturing Business
The tire industry is always changing. To stay ahead, you need to use the latest ERP solutions. This helps your business grow and keep up with new technologies.
Scalability and Growth Management
As your business gets bigger, your ERP system needs to grow too. Look for systems like Microsoft Dynamics that can scale with you. They help you manage your production, inventory, and customer needs better.
With the right ERP, you can make your processes more efficient. This sets your business up for long-term success.
Forecasting and Trend Analysis
With the data from their ERP systems, tire makers can use advanced forecasting and trend analysis. These tools help predict market needs and plan production. By studying past trends, tire makers can get ready for changes in demand and adjust their operations.
Using data-driven decision making in tire industry ERP solutions helps businesses adapt fast to market changes. This leads to better processes and growth. By using analytics, reporting, forecasting, and trend analysis, tire makers can make smart decisions. This improves their efficiency and profit.
Emerging Technology Integration
The tire industry is adopting new technologies fast. This includes advanced analytics, automation, IoT, and AI. By linking your ERP to these technologies, you can improve your operations and make better decisions.
Microsoft Dynamics makes it easy to connect with these tools. This keeps your business leading the way in the industry.
For DSI, PentagonIT Solutions implemented a specialized planning and scheduling solution, streamlining production with advanced digital tools. Check out the full case study here.