- Home
- Printing and Packaging
Printing and Packaging
Corrugation Industry ERP Solution
ERP solution, specially developed for the Corrugation industry needs
Boxes have always reigned as the numero-uno preferred form of transport packaging. Whether it is to display, promote, or package, there is corrugated material in anything we buy and see. As it is said, boxes are so ordinary. Covid times, war times, or regular times, the industry has to keep the supply chain running either for everything or the makers of the essential goods.
The Corrugated Packaging Industry faces intense competitive pressures, commoditization, stringent compliance, and audit procedures, as demanded by leading brand owners. Besides the high input costs, like all other industries, the Corrugated Packaging industry is undergoing massive and rapid cultural change.
Our solution to the corrugation industry facilitates all of the above to ensure it’s the best fit to aid you in navigating the rough waters and understanding the dynamics of the industry to adapt as demanded.
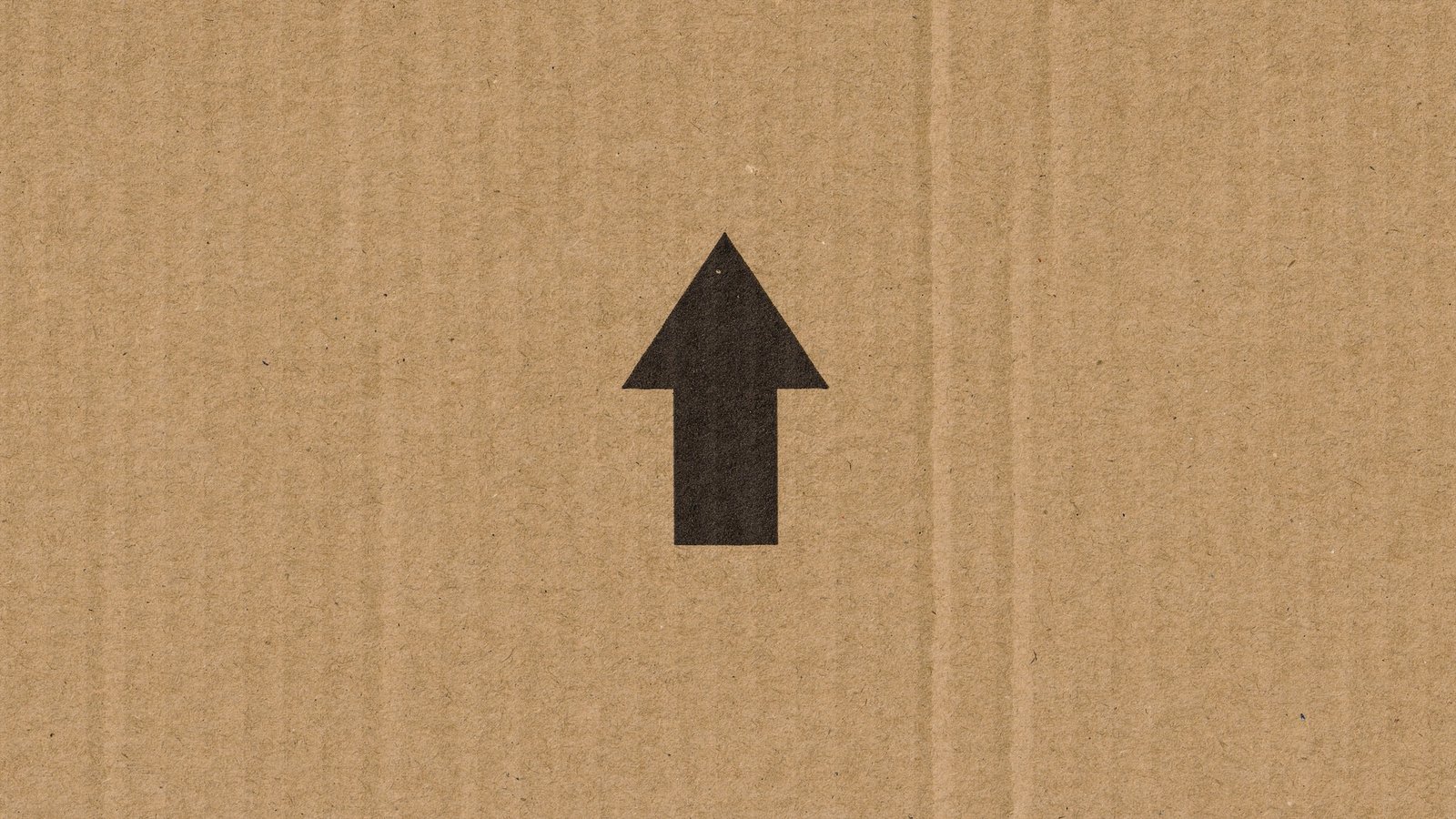
Features of Printing and Packaging
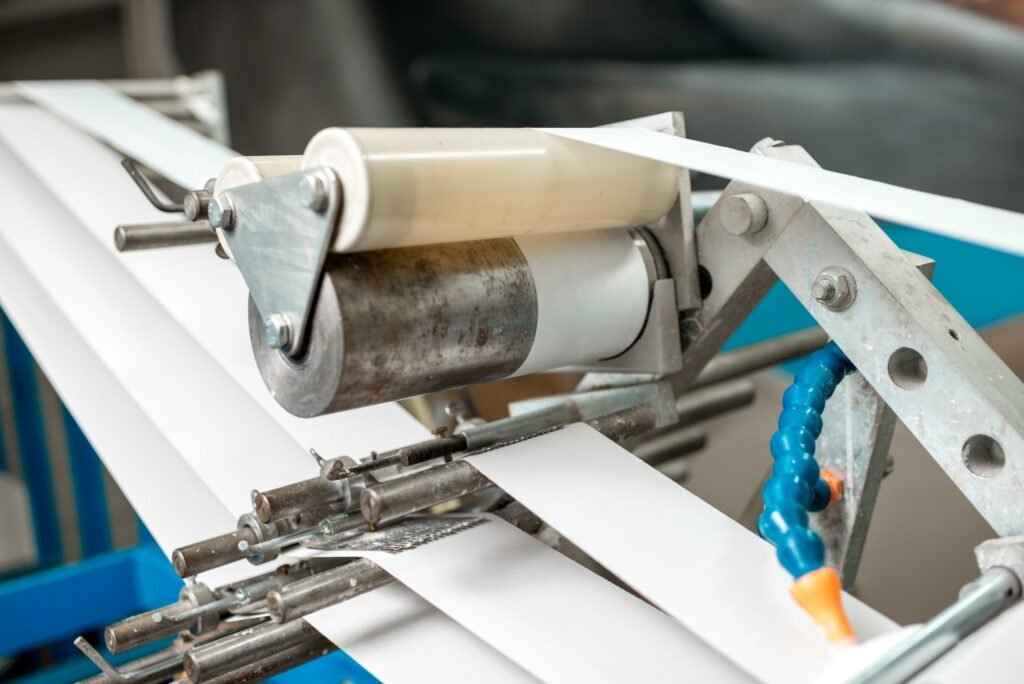
Why PIR paper
What do we offer for this industry
- Boost Operational Efficiencies
- Packing and Loading Optimization
- AI driven Production Planning & Scheduling
- Manage your Enterprise Planning effectively
- Single source of truth
ExPack Case Study
Over 100+ Clients
Join 100+ industry giants who’ve reached us
Few of the 100s of our beloved clients who have been with us for years
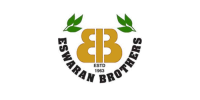
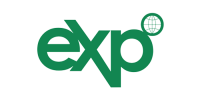
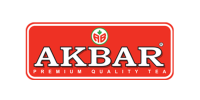
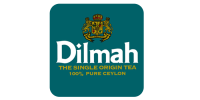
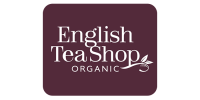
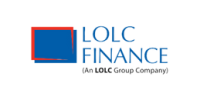
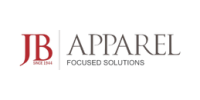
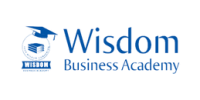
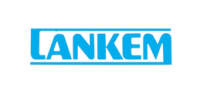
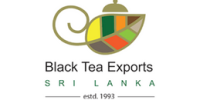
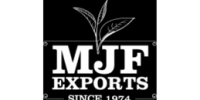
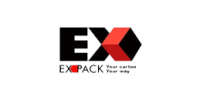
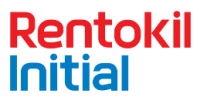
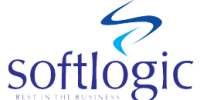
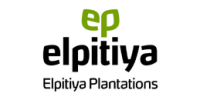
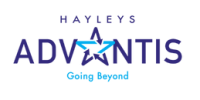
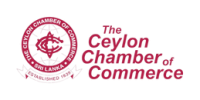

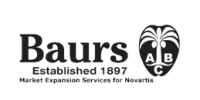
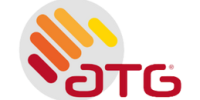
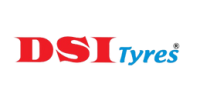
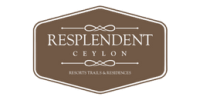