- Home
- Process Manufacturing
Process Manufacturing
Manufacturing ERP Solution
ERP solution, specially developed for the Manufacturing industry needs
Process manufacturing is a production method that creates goods by combining raw materials, ingredients, or substances through a series of chemical, biological, or mechanical processes. This method is commonly used to produce bulk quantities of items such as chemicals, pharmaceuticals, food and beverages, petroleum products, and other materials that are typically homogeneous and cannot be easily disassembled into their basic components. Unlike discrete manufacturing, which produces distinct items like cars or computers, process manufacturing involves continuous or batch production where the final product is often the result of blending, mixing, heating, or chemical reactions. This manufacturing approach requires precise control over variables such as temperature, pressure, and ingredient ratios to ensure consistent product quality and compliance with industry standards.
At Pentagon IT Runway, we understand the complexities and unique demands of the process manufacturing industry. Whether you’re producing chemicals, pharmaceuticals, food and beverages, or other bulk goods, our advanced ERP and Siemens Advanced Planning and Scheduling software solutions are designed to streamline your operations and boost efficiency.
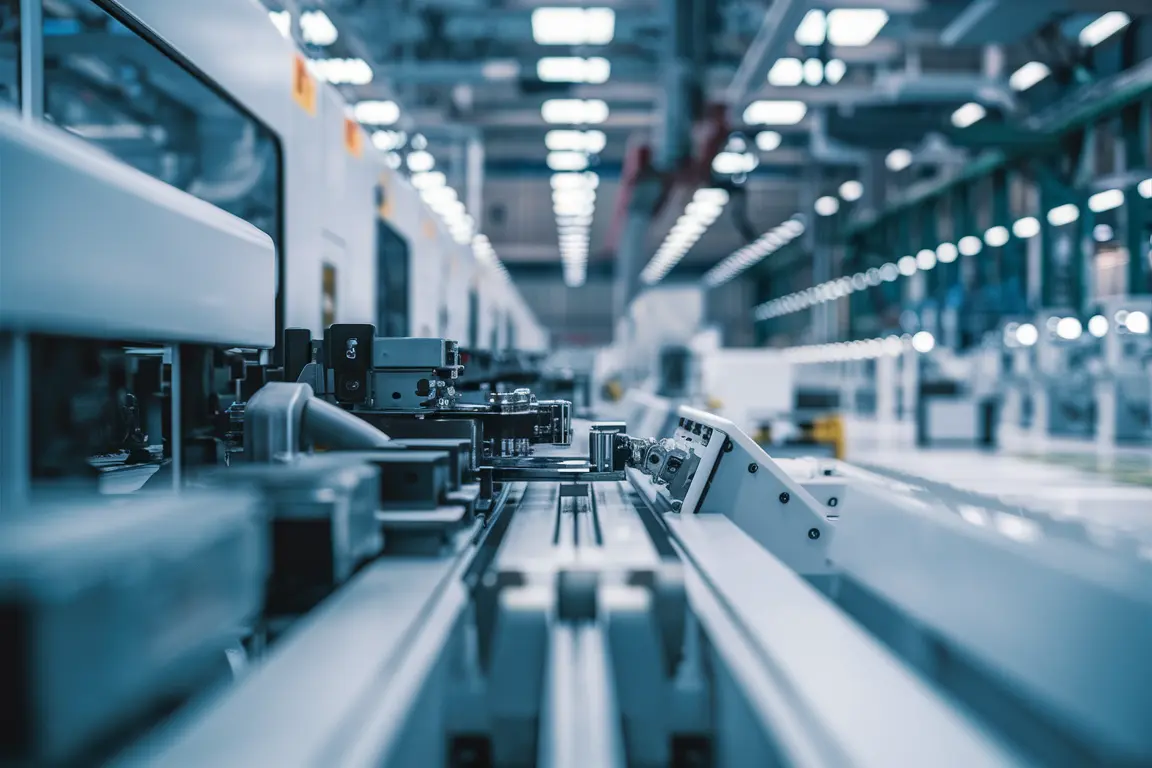
Features of Process Manufacturing
Over 100+ Clients
Join 100+ industry giants who’ve reached us
Few of the 100s of our beloved clients who have been with us for years
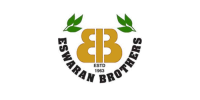
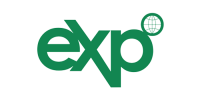
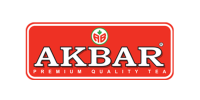
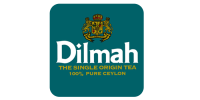
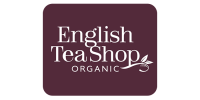
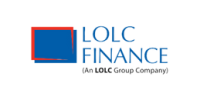
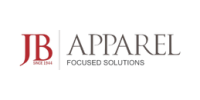
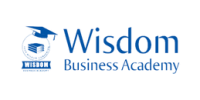
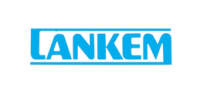
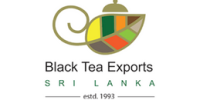
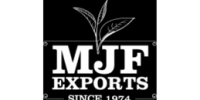
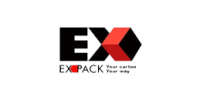
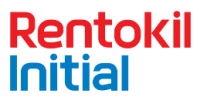
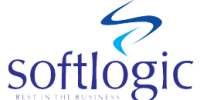
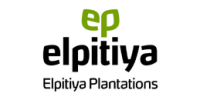
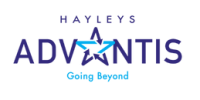
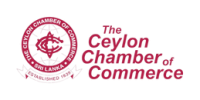

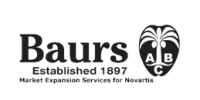
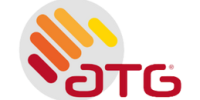
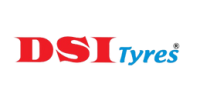
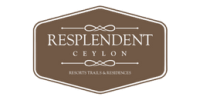