The food and beverage (F&B) industry thrives on precision, efficiency, and innovation. From the initial procurement of raw materials to delivering finished products to customers, every step in the production process requires meticulous planning and execution. Managing this intricate lifecycle effectively is key to maintaining product quality, reducing costs, and meeting consumer expectations. Let’s explore how cutting-edge solutions are revolutionizing the way F&B manufacturers approach production management, from auction catalogs to the dinner table.
The Starting Point: Raw Material Procurement
In the F&B industry, the journey begins with sourcing raw materials. Whether it’s selecting coffee beans from an auction catalog, purchasing grains, or acquiring fresh produce, this phase sets the tone for the entire production process. Modern systems enable manufacturers to integrate procurement data directly into their operational workflows, ensuring they have real-time access to pricing, quality specifications, and availability. By digitizing this stage, businesses can:
-
Compare multiple suppliers quickly and efficiently.
-
Ensure transparency in pricing and quality standards.
-
Forecast procurement needs based on historical and seasonal data.
Blending for Perfection
Blending raw materials is a cornerstone of F&B production. For example, coffee roasters and tea manufacturers must achieve consistent flavors by blending various beans or leaves. Advanced production solutions simplify this process by allowing manufacturers to simulate blend outcomes before production begins. Using these tools, businesses can:
-
Test different blend ratios virtually to achieve desired quality.
-
Track the exact composition of each blend for regulatory and customer transparency.
-
Minimize waste by optimizing ingredient usage.
Sieving and Quality Control
Bulk processing involves scaling up production while maintaining quality. This stage is critical for meeting market demand efficiently. Modern manufacturing platforms integrate bulk processing with workflow management tools, allowing manufacturers to:
Optimize production schedules for maximum efficiency.
Track each batch through every stage of production.
Reduce downtime with predictive maintenance alerts for machinery.
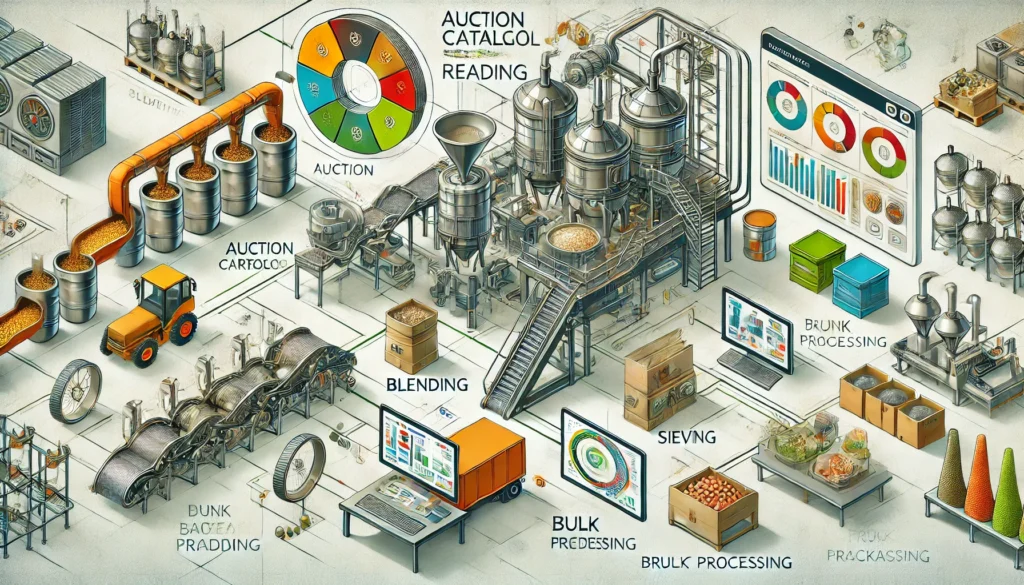
Addressing Blend Gain and Loss
One of the biggest challenges in F&B production is managing blend gain and loss. Inefficiencies during blending or processing can lead to discrepancies between input and output quantities, resulting in higher costs and lower profitability. Advanced systems provide precise tracking of materials through the entire production process, helping manufacturers:
-
Identify and address sources of material loss.
-
Ensure accurate inventory management.
-
Reduce waste, contributing to sustainability goals.
Adding Value to Your Product
Value-added processes, such as packaging, fortification, or flavor enhancement, are critical for creating products that stand out in a competitive market. These processes often require synchronization with the rest of the production workflow. Integrated solutions empower manufacturers to:
Customize packaging based on market or customer requirements.
Implement quality checks at every stage to ensure consistency.
Streamline value-added steps to reduce lead times.
The Role of Advanced Planning and Scheduling
Production planning and scheduling are the backbone of efficient manufacturing. In the F&B sector, where margins are often tight, the ability to optimize resources and workflows can make all the difference. Advanced planning and scheduling tools offer:
-
Visual, user-friendly interfaces for intuitive production management.
-
Real-time adjustments to accommodate unforeseen changes, such as equipment downtime or supply chain disruptions.
-
Forecasting capabilities to align production with market demand.
Harnessing Business Intelligence for Smarter Decisions
Data is a powerful asset in the modern F&B industry. Business intelligence tools enable manufacturers to turn raw data into actionable insights, helping them make informed decisions at every stage. Key benefits include:
-
Tracking production KPIs, such as yield, efficiency, and waste.
-
Identifying trends and patterns to optimize future operations.
-
Providing transparency for stakeholders, from suppliers to end consumers.
The Price Simulator: A Unique Advantage
One of the most innovative advancements in F&B production is the development of price simulation tools. These tools allow manufacturers to calculate the full cost of production, factoring in raw materials, labor, energy, and overheads. With this capability, businesses can:
Accurately price products to maintain profitability.
Identify cost-saving opportunities without compromising quality.
Stay competitive in a dynamic market by quickly adjusting pricing strategies.
Building Resilience with Industry 4.0
The F&B industry is rapidly embracing Industry 4.0 principles, leveraging automation, IoT, and data analytics to create smart factories. These technologies enable manufacturers to:
-
Monitor equipment and production lines in real-time.
-
Implement predictive maintenance to avoid unexpected downtime.
-
Enhance traceability, ensuring that every product’s journey from raw material to finished goods is transparent and compliant with regulations.
Conclusion
Managing the full lifecycle of F&B production is a complex endeavor, but modern solutions have made it more efficient and effective than ever. By integrating advanced tools for procurement, blending, quality control, and bulk processing, manufacturers can streamline operations, reduce costs, and deliver high-quality products that meet consumer expectations. With the right systems in place, the journey from auction catalogs to the dinner table becomes not only manageable but a source of competitive advantage.
The future of F&B production lies in embracing innovation and leveraging technology to transform challenges into opportunities. Whether you’re a small producer or a large-scale manufacturer, investing in comprehensive production management tools will empower you to thrive in a competitive and ever-evolving industry.