In today’s highly competitive manufacturing landscape, staying ahead requires more than efficient machinery and skilled labor—it demands smarter planning and real-time adaptability. Advanced Planning and Scheduling (APS) software has emerged as a game-changing tool that revolutionizes production scheduling, enabling manufacturers to optimize resources while minimizing costs and delays. For organizations embracing Lean Manufacturing principles, APS bridges the gap between traditional Just-in-Time (JIT) practices and the flexibility of Agile Production.
Understanding APS and Its Role in Modern Manufacturing
APS systems are sophisticated tools that leverage advanced algorithms to optimize production schedules. Unlike traditional Enterprise Resource Planning (ERP) systems that rely on fixed lead times and static scheduling rules, APS systems dynamically adjust to constraints, such as machine availability, labor capacity, and material supply. This ability to account for real-world complexities makes APS invaluable for manufacturers seeking continuous improvement.
Key features of APS include:
Real-time production scheduling and rescheduling
Multi-constraint optimization (labor, materials, equipment)
Scenario-based planning to evaluate different scheduling outcomes
By integrating APS into their operations, manufacturers can maximize throughput, reduce waste, and improve customer service levels—all critical tenets of Lean Manufacturing.
Lean Manufacturing and Its Core Principles
Lean Manufacturing, popularized by the Toyota Production System, focuses on reducing waste and increasing value delivery to customers. Key principles include:
Value Identification: Defining value from the customer’s perspective.
Value Stream Mapping: Analyzing workflows to identify and eliminate waste.
Flow Optimization: Ensuring a smooth, uninterrupted flow of production.
Pull Systems (JIT): Producing only what is needed, when it is needed.
Continuous Improvement (Kaizen): Regularly refining processes to enhance efficiency.
While Lean aims to create a seamless, waste-free production system, its implementation can be challenging due to variability in demand, supply chain disruptions, and resource limitations. This is where APS technology proves invaluable.
APS and Just-in-Time: A Perfect Match
Just-in-Time (JIT) manufacturing, a cornerstone of Lean, emphasizes producing only what is needed to fulfill current demand. While JIT minimizes inventory costs, it requires precise scheduling to avoid stockouts or production halts. APS enhances JIT strategies by:
Managing Variability: APS systems predict fluctuations in demand and adjust schedules accordingly, reducing the risk of overproduction or stockouts.
Real-Time Rescheduling: If a machine breakdown or supply delay occurs, APS can instantly generate a new schedule, ensuring minimal disruption.
Synchronizing Supply Chains: APS improves collaboration between suppliers and production lines by aligning material deliveries with production needs.
By integrating APS into a JIT environment, manufacturers can achieve greater precision and resilience, maintaining lean inventory levels without sacrificing reliability.
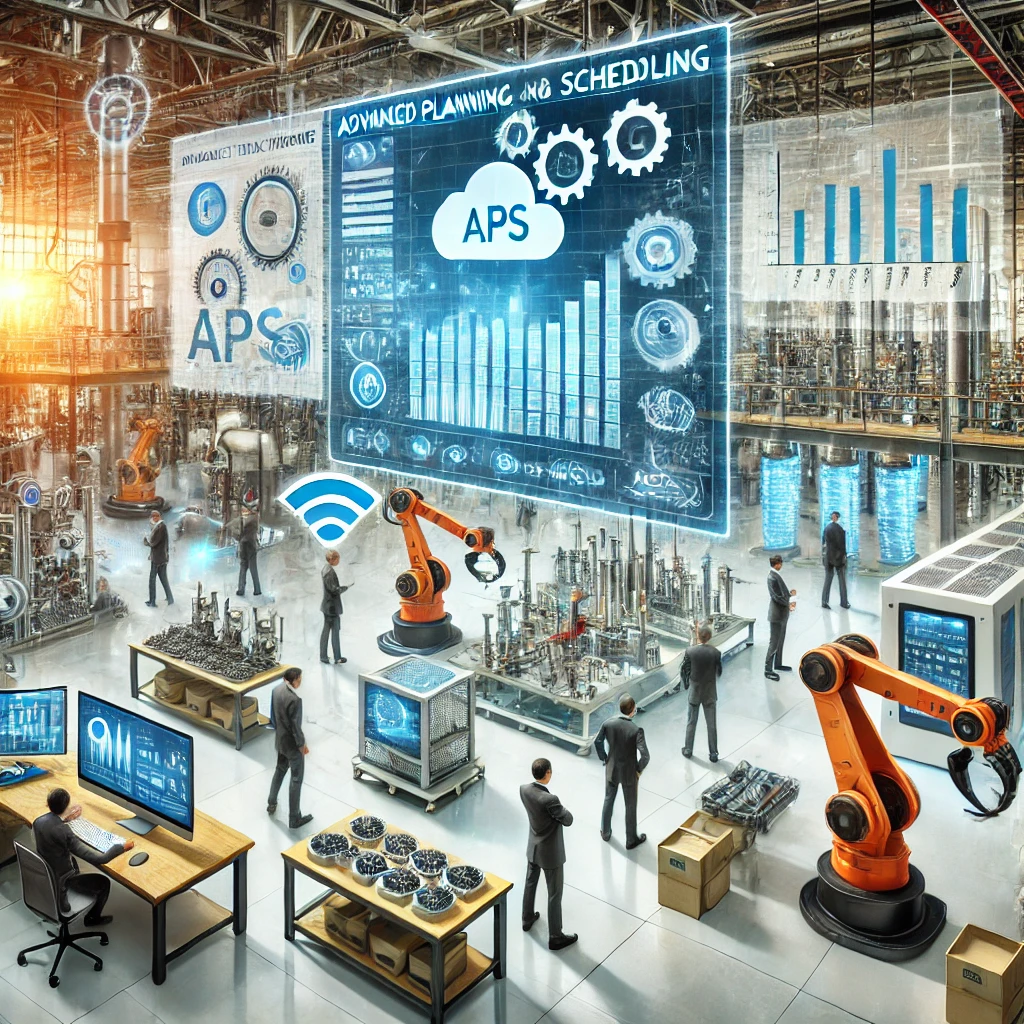
APS Supports Agile Production
Agile Production emphasizes flexibility and responsiveness to changing customer demands. Unlike Lean’s traditional focus on efficiency, Agile prioritizes adaptability. APS bridges these two approaches by offering real-time insights and predictive analytics that allow manufacturers to quickly pivot when:
Order Priorities Shift: APS automatically reorders production tasks to meet urgent orders without disrupting overall efficiency.
New Product Introductions: Rapidly adjusting schedules for prototype runs or new product lines.
Demand Spikes or Declines: Predictive algorithms model multiple demand scenarios to prepare for fluctuating production volumes.
With APS, Lean manufacturers can adopt Agile practices without compromising their commitment to waste reduction and flow optimization.
Scenario-Based Planning for Continuous Improvement
A hallmark of APS systems is their ability to simulate various production scenarios. This feature empowers manufacturers to experiment with different strategies before implementing them on the shop floor, facilitating continuous improvement. For example:
What-If Analysis: Evaluating the impact of adding a new shift or purchasing additional equipment.
Constraint-Based Optimization: Identifying bottlenecks and testing solutions to improve throughput.
Lead Time Reduction: Experimenting with different batch sizes to minimize delays.
These capabilities align with Lean’s Kaizen philosophy by enabling data-driven decision-making and incremental improvements.
The Future of APS and Lean Manufacturing
As technology advances, APS systems are evolving with artificial intelligence (AI) and machine learning (ML) capabilities. Predictive analytics, enhanced by AI, can forecast demand patterns with greater accuracy, while ML algorithms continuously refine scheduling strategies based on historical performance data.
Emerging trends include:
-
Cloud-Based APS Solutions: Offering scalability and seamless integration with existing ERP systems.
-
IoT-Enabled Smart Factories: APS systems interfacing with IoT devices to receive real-time data from production equipment.
-
AI-Driven Predictive Maintenance: Using APS to schedule proactive maintenance, reducing unplanned downtime.
These innovations will further strengthen the synergy between APS and Lean Manufacturing, helping manufacturers remain competitive in a rapidly changing marketplace.
Conclusion
Advanced Planning and Scheduling (APS) software is a powerful tool that enhances Lean Manufacturing by addressing its inherent challenges with variability and adaptability. By seamlessly integrating with JIT systems and enabling Agile practices, APS empowers manufacturers to optimize production, reduce waste, and improve customer satisfaction. As technology continues to evolve, the integration of AI and IoT will unlock new levels of efficiency, making APS an indispensable component of the future manufacturing landscape.